How to reduce the gap between theoretical and actual building performance
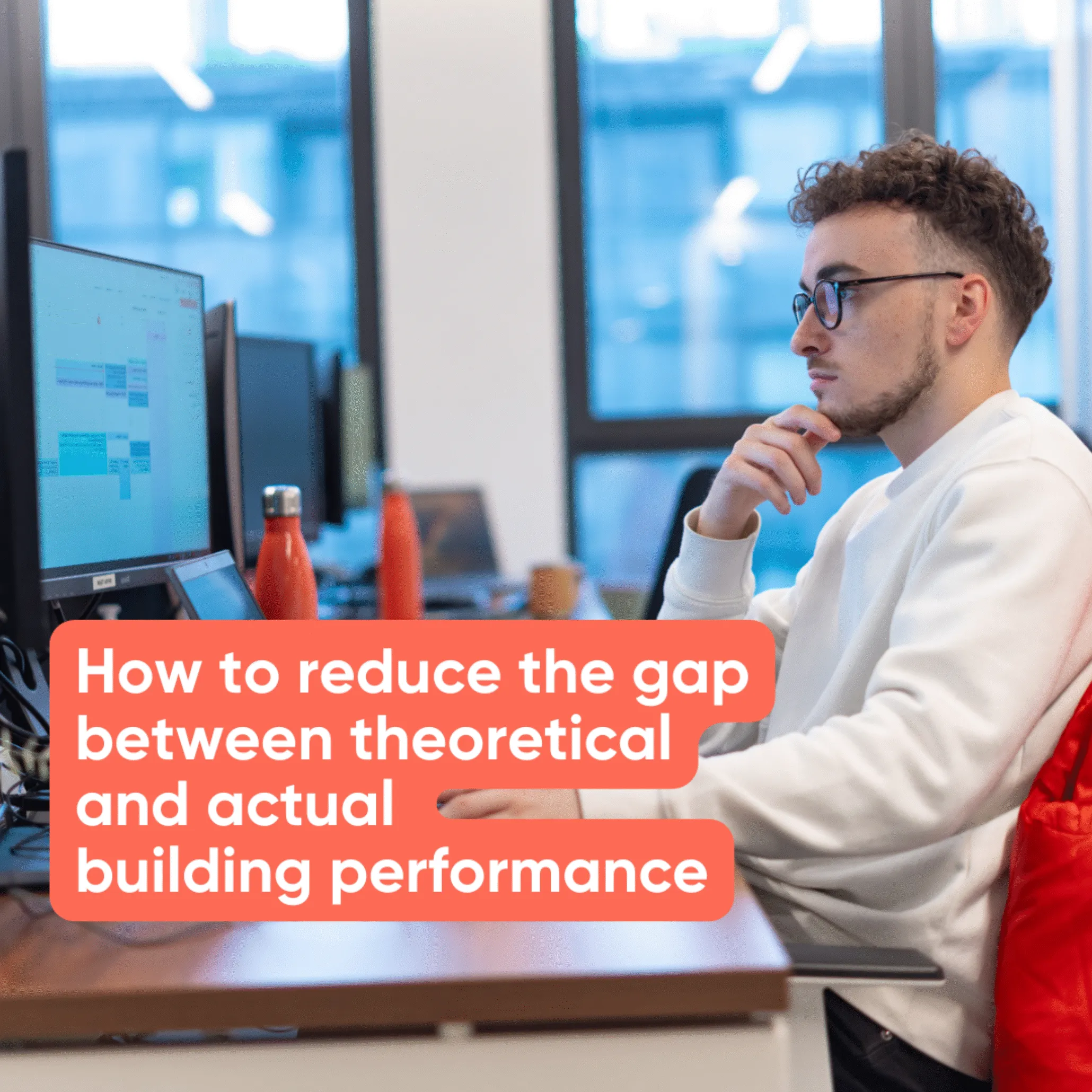
The building sector plays a central role in the United Kingdom’s energy transition. To achieve carbon neutrality by 2050, the country has set a target to reduce its greenhouse gas emissions by 78% by 2035. As part of this effort, the Building Regulations Part L (2021) have strengthened energy performance requirements for new constructions and renovations.
However, a major challenge remains in practice: the gap between the projected energy performance at the design stage (regulatory calculations, thermal modeling) and the actual performance during operation. This gap, often underestimated, can reach between 20% and 60%, affecting energy consumption, operating costs, and the ESG objectives of real estate portfolios.
How can this phenomenon be explained, and more importantly: how can it be effectively reduced?
1. A Systemic Issue Rooted in the Design Phase
In many projects, mandatory thermal simulations are carried out during the building permit phase but are rarely updated thereafter. However, the gap between initial assumptions (weather conditions, usage patterns, equipment) and operational reality can be significant.
Moreover, modeling tools do not always account for:
- variations in occupant behavior,
- discrepancies between the performance of installed equipment and that initially planned,
- or the margin of error associated with the commissioning and configuration of technical systems.
2. Commissioning: A Critical but Often Overlooked Step
Commissioning (the technical commissioning of the building) is a crucial phase to ensure that the building operates as it was designed. Yet, it is still too often treated as a mere formality.
High-quality commissioning allows:
- verifying the installation and proper configuration of HVAC systems, BMS, lighting, etc.,
- identifying failures or deviations before handover,
- training operators to ensure effective building management.
In projects aligned with Net Zero objectives, this step becomes essential to guarantee measurable and achievable energy performance.
3. Real-World Measurement: An Essential Lever
The only reliable way to assess a building’s performance is to measure its actual consumption under operating conditions. This requires:
- implementing an appropriate energy sub-metering system,
- having data structured by usage (heating, DHW, ventilation, lighting, etc.),
- being able to compare actual consumption to projections.
This approach makes it possible to quantify the real gap but, more importantly, to quickly correct any deviations. Many managers now use cloud-based solutions or IoT platforms to automate this analysis.
4. Close Collaboration Between All Stakeholders
Reducing the gap between theoretical and actual performance requires the collaboration of:
- designers (architects, engineering consultants),
- installers,
- commissioning managers,
- operators and Energy Managers.
It is through this collaborative approach that energy continuity can be built throughout the building’s lifecycle, from construction to long-term operation.
Bridging the gap between calculated and actual performance is much more than a technical challenge — it is a strategic opportunity in the UK market.
- Operating cost optimization: Controlled performance helps secure operating expenses and quickly achieve savings on consumption.
- Improvement of EPC ratings: Better control of actual consumption makes it easier to meet regulatory thresholds required for the leasing or resale of assets.
- ESG value enhancement: Investors and buyers are increasingly seeking buildings with measured, monitored, and Net Zero-compliant performance.
- Access to sustainable financing: Many banks and funds condition their “green” loans on proof of verified, real-world performance.
In short: closing the gap between theory and reality secures investments, strengthens the green value of assets, and anticipates future market demands.